Forrest Burney isn’t a SimApp salesman, or any kind of salesman actually, but he’d certainly make a good one. Burney is the Engineering Manager of Plastics at BWay Corporation, one of the largest manufacturers of packaging containers for industrial, commercial and retail markets in North America.
Salesperson or not, Burney unfurled a pretty convincing testimonial recently during an NAFEMS (National Agency for Finite Element Methods and Standards) webinar titled Democratization: Accessibility about how BWay Corporation is starting to use, and benefit from, computer-aided engineering (CAE) simulation applications (SimApps).
Burney was one of two “User Stories” during the presentation, which also included a demonstration by Jeffrey Crompton, principal of AltaSim Technologies, of a HeatSinkSim app. These two stories were obviously interesting to us because both BWay, which partners with Comet Solutions and Kinetic Vision, and AltaSim partner with AweSim at OSC. OSC has a history of industrial engagement beginning with our charter through Blue Collar Computing and now the AweSim project.
This week’s webinar, part of NAFEMS’ 2020 Series, focused on CAE accessibility issues while shining a light on how engineers can benefit from simulation apps.
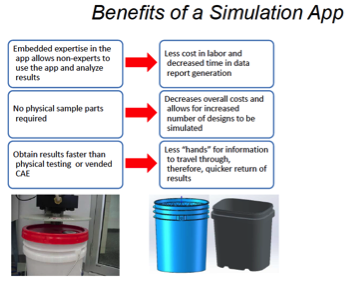
According to Burney’s presentation, which showed the evolution of BWay’s product development through the years, SimApps will make his life much easier while directly impacting the companies’ bottom line in a major way.
In three slides, Burney illustrated the processes BWay used prior to 2005, from 2005-2015 and from 2015-onward, which now includes the SimApp process. It’s a pretty compelling look at how the company has gone from an expensive and lengthy trial-and-error process to make the molds that produce the products to the SimApp process.
“We have an app on the cloud we put our product design into very easily and quickly,” Burney said. “Instead of a handful of iterations, we can use the apps and submit many iterations and really zero in on a product design and optimize it as much as possible before we ever cut steel on a mold. Typically it’s one and done, or two and done and we’ve got a product out in the marketplace.”
The time-to-market is much quicker and the savings of not constantly making new molds can be anywhere from $5,000 to $40,000 when compared to BWay’s pre-2005 process.
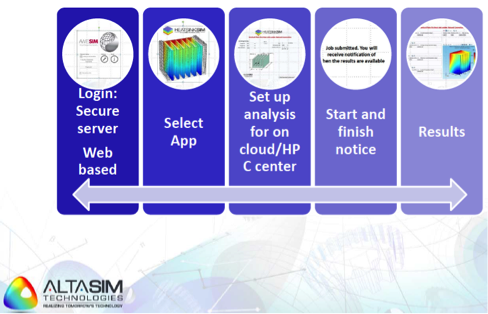
Burney was followed by Crompton, who discussed the need for increased accessibility to computational simulation apps along with modeling and simulation software for smaller- and medium-sized enterprises. He then demonstrated the HeatSinkSim app – an app used for providing temperature control of electronic control systems. It’s a process that basically boils down to logging in, inputting the numbers and getting an email once the results are done.
Both of these end-user stories are so consistent with what we hear on a regular basis and we recommend you check the webinar recording today. It’s only an hour but could certainly be helpful in illustrating the quicker time-to-market and the high return on investment companies are seeing with modeling and simulation.
If you’d like to learn more about AweSim feel free to contact us today. We welcome the opportunity to work with medium- and small-manufacturers, and companies of all shapes and sizes, to improve their product workflow and we’d love to hear from you on how we can help today.